The pulp molding machinecomprises a set of machinery aimed at recycling waste paper. Improper disposal of these items results in pollution. Through a systematic and extensive process, the device turns waste into an array of valuable products, including trays for eggs, shoes, fruits, and coffee cups. Currently, there are numerous options for the appliance for all kinds of investors. Whether you are in a small scale or industrial business, you have an opportunity to join the lucrative production(maquina para hacer cartones de huevo) . Understanding the step-by-step operations of the machine is a gateway to achieving your goals and settling for the best in the market. Below is detailed information on the processes.
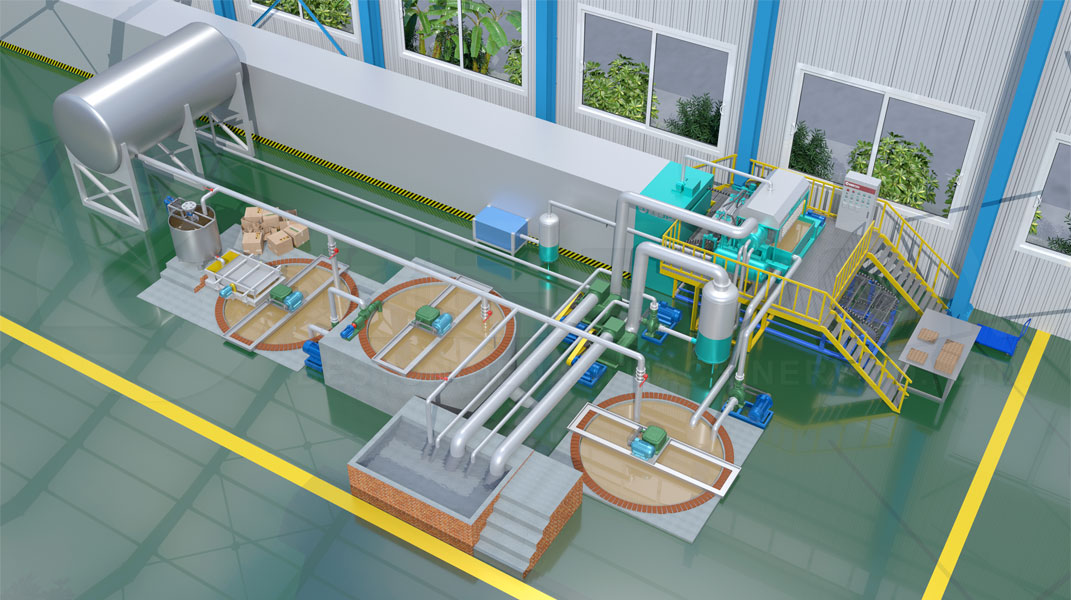
Máquina para Hacer Bandejas del Huevo
Pulping.
The first step of production is pulping. Pulping refers to mixing the primary raw material, waste paper, and water to form one consistent mix, pulp. The molding system features an open area for mixing the items, a pulp beater, and a water source. The operator combines the appropriate amounts of each product. Otherwise, there would be a waste, and the mix wouldn’t be consistent. The goal is to avoid having a thick or runny mixture. Upon mixing, the pulp(maquina de hacer maples de huevo) beater thoroughly combines the items to eliminate any lumps. You can also add pigmentation if necessary and additives for longer shelf life. Upon completion, the mix gets transferred to standby pipes.
Molding.
The second phase involves molding the already formed pulp into desirable shapes as per the customer’s demand. The molding system features a vacuum pump, an air compressor, developing and moving molds. The pulp molding machine forms a comprehensive range of end products thanks to the availability of different molds. The operators fix all the relevant models and then discharge the pulp from the pipes. The mix lands on the items until they’re fully covered. The next step is using the vacuum pump to suck out any air and remove excess water for the efficiency of the subsequent procedure. This stage is vital since the operator can establish the quantity of production. Keen attention is paramount to ensure there are no inaccuracies. The final part of this phase is detaching the products by blowing air using the compressor.
Drying.
Although the vacuum pump gets rid of some water, the products still retain some moisture, thus exposing them to heat. The pulp molding machine (https://www.bestoneco.com/maquina-para-hacer-bandejas-de-huevos/)employs three distinct types of drying systems. The first and most affordable is natural dying under the sun. The second is the brick drying line and lastly metal drying system. Each option works towards a similar goal, but the choice varies depending on certain aspects. The first option is cheap but suitable for small-scale operations. The others are costly but convenient.
Packaging.
After drying follows packaging. However, you must first pass the output through a hot press for better defining. The process also helps in stacking a huge number hence saving storage material.
The pulp molding plant is an ideal venture with the potential to earn you profits. Its production mechanism(Grupo Beston) is safe and affordable, with no emissions and limited wastages.